[center]
CHAPTER III - Chassis building & structure supporting
[/center]
As long I decide to build the kit straight from the box, without interior details and keeping all hatches closed, I placed a styrene plastic sheet to keep driver's hatch isolated. The reason will be explained later.
[center]
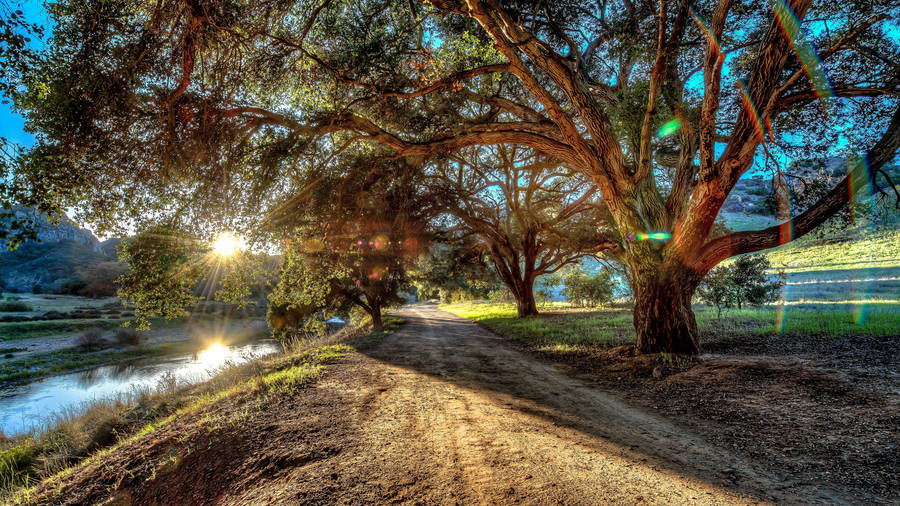
[/center]
The
HPX, is one of the most durable adhesive tape that can be found on the local market. It is vinyl reinforced multi-purpose pressure sensitive tape with a soft and flexible shell and pressure sensitive adhesive. It is generally silver or black in color but many other colors have recently become available. With a standard width of 50mm (approx 2 inches) & 0.30mm thickness, water resistant & withstand temperature ranges from Fahrenheit -40° to Fahrenheit 203° is ideal for special purposes. It is constructed from a rubber-based adhesive to help the tape resist water and a fabric backing to add strength. Keep in mind that US Military issued this hard duty adhesive tape to their personnel who keep it in their pack and use it in numerous cases, such as repairing scratches, temporarily taping holes on aircrafts or helicopters fuselage, ammo canisters sealing, repairing military equipment (including firearms) quickly etc. Click
HERE for aircraft repair with adhesive tape example. In military circles, this variant is known as "gun-tape", typically olive-green, and also known for its resistance to oils and greases. It is also called "Riggers Tape", "Hurricane Tape", or "100-mph tape" - a name that comes from the use of a specific variety of duct tape that was supposed to hold up to 100 mph winds. Another version attributes this to the fact that soldiers often refer to something that exceeds expectations as "High Speed". The HEX tape is commercially sold as high-strength adhesive tape for sealing tire tubes aquifers.
[center]
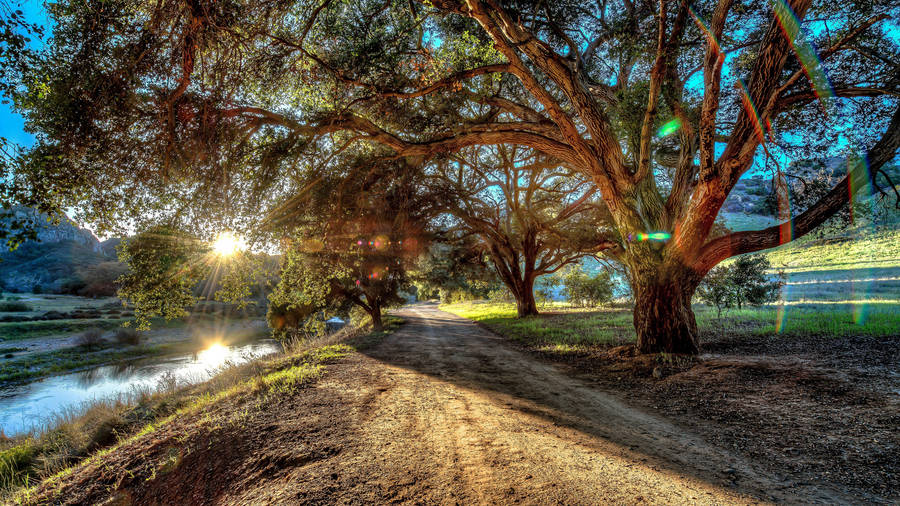
[/center]
Before trying to connect FDCV's main chassis, I stretched tape inside the two halves. As it is known, polyester loses its elasticity and becomes harder, several months or years after casting and vibrations could cause cracking. The polyester made models do not have the durability of plastic because the different chemical composition and molecular bonds of each material. Over time, polyester behaves like glass, although it has toughness, but any hard vibration could cause crack or even worse shattering. Placing HPX durable adhesive tape inside, would hold the spread of a possible crack in the future, provide the opportunity to fix and save the scale model. In all other cases, the polyester fragments would be lost. Placing HPX durable adhesive tape inside, is the first of few precautionary measures taken for the integrity of the material. The next and most important precautionary measure, will be described into following paragraphs.
[center]
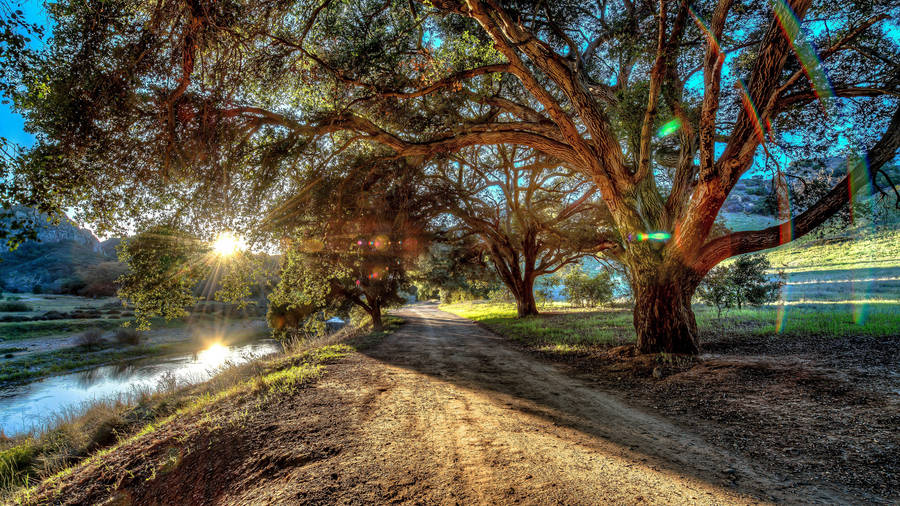
[/center]
To be honest, I thought that when the time comes to connect the chassis two halves, I would face plenty of problems. Let's not forget that this specific kit is made of polyester resin, rather than an injection molded Japanese plastic with excellent quality and factory mass production of tens of thousands of kits. This is actually a handmade kit, molded in silicon. After carefully cleaned from the polyester casting excess in contact points between the chassis two halves, I tried repeatedly to contact each other to be sure that I will not face any unpleasant surprises after applying super glue. To make the job easier, the chassis two halves dipped in hot water for 1-2 minutes to obtain polyester flexibility (which lasted for the few critical minutes) and to assist my effort to buckle one part into the other. That's why the adhesive tape used and described previously, was the HPX product with high temperature & water resistance - if I would try a simple cheap tape, it would just come off as soon as the polyester kit parts immersed into hot water. Same elasticity effect on polyester could be achieved using a hair dryer and guiding hot air on selected spots. When the two halves buckled together, I dropped cyanoacrylate glue on all four corners and later secured the construction stability by applying two components super glue, across the chassis two halves contact line, using a wooden toothpick.
[center]
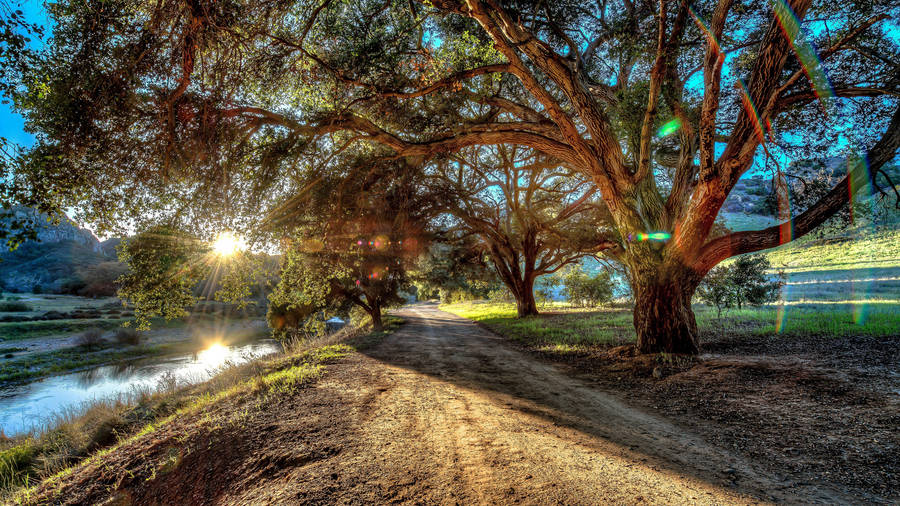
[/center]
I am not used to fill gaps with simple modelling putty, since I prefer a two-component epoxy or polyester putty. As mentioned into previous paragraphs, I mostly prefer to use epoxy putty (or polyester filler with fiberglass grains for special purposes) instead of normal scale modeling putty, to close gaps or build new items.
[center]
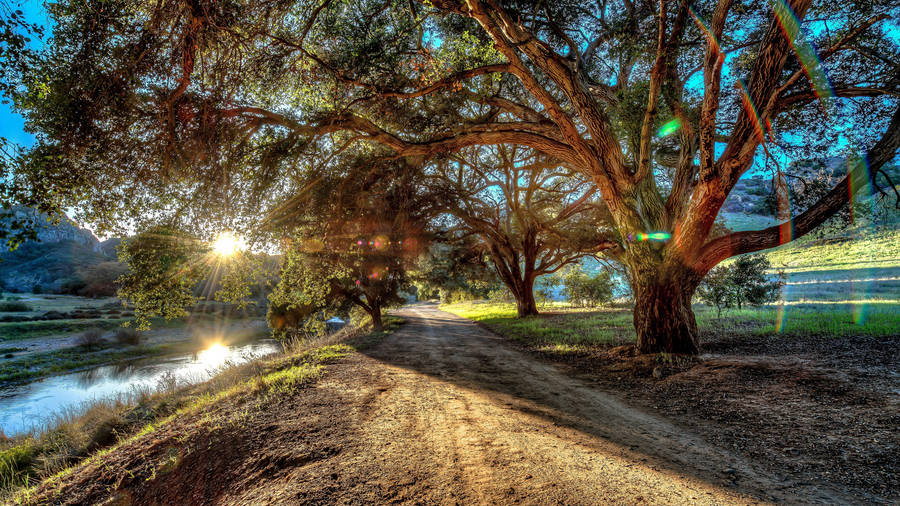
[/center]
Just because this is a polyester kit and the material does not get affected and does not get damaged by the nitrocellulose lacquer thinner, I thought nice idea to follow something different. I tried spreading Humbrol simple modelling putty on the gap, and applied generous amounts of nitrocellulose lacquer thinner on Humbrol putty, to get it soften, turn it into semi-liquid form and smoothly spread it across the chassis two halves contact line.
[center]
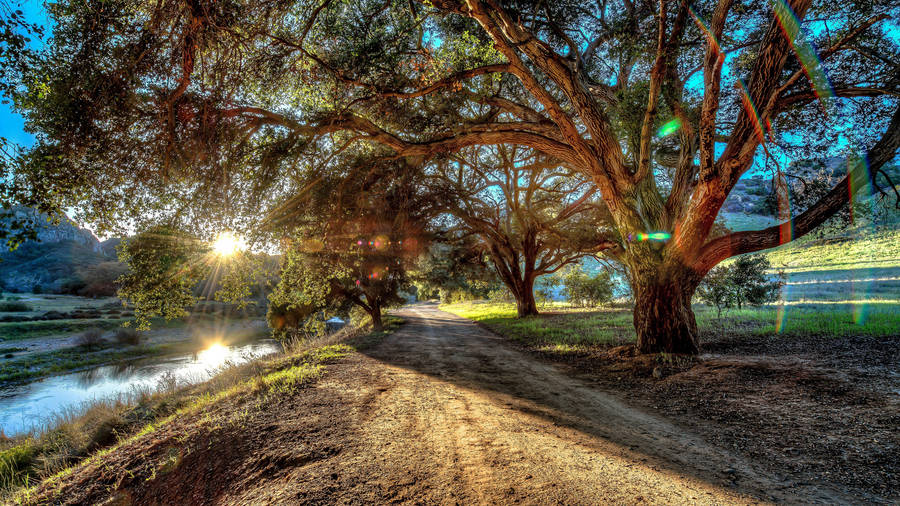
[/center]
Finally, only few drops of nitrocellulose lacquer thinner on small amount of Humbrol modelling putty, was enough to create a liquid solution to spread with brush across the chassis two halves contact line.
[center]
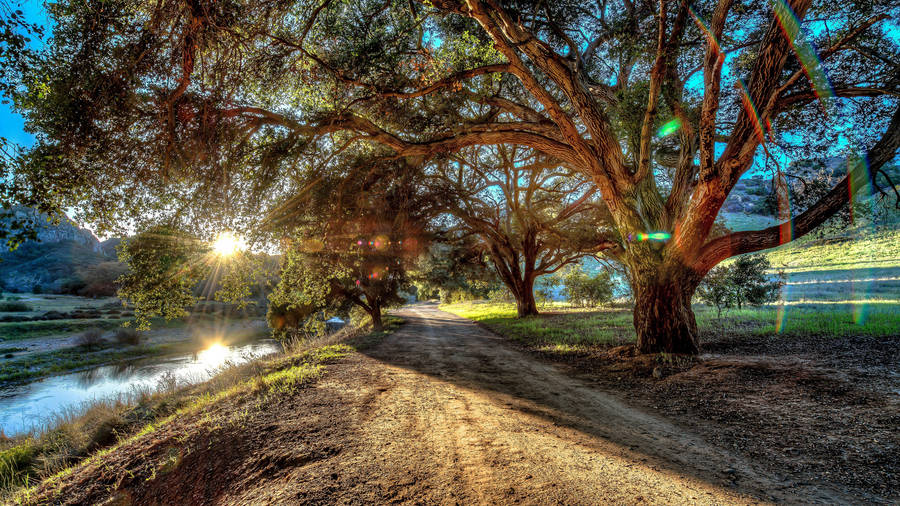
[/center]
As noted before, polyester loses its elasticity over time and the slightest shock, bang or hard vibration during model transporting may cause a crack. To reduce the danger of such an unfortunate situation and as a part of precautionary measures to strengthen the structure of the polyester model, I decided it would be nice to fill the internal model with the material that should be:
- Solid and able to occupy all the available volume inside the model, supporting internally the walls of the polyester model,
- As light as possible to avoid model’s total weight increasing that could strain the wheel polyester arms,
- Hard, but not completely rigid, that can absorb vibrations & shocks and able to transmit vibrations soflty, throughout model’s mass and not on a single point.
This material is called polyurethane foam. It is a unique industrial material which has excellent physical, mechanical and environmental properties and is mainly used as insulation material. It offers high abrasion resistance, tensile stress, impact resistance etc. The fact that the polyurethane foam material can be easily cut, sawed, sanded, drilled etc and is compatible with most types of scale modelling glue & any type of primer or enamel / acrylic paint with no problem at all, makes it a good choice for many scale modelling applications, as for example in diorama building.
[center]
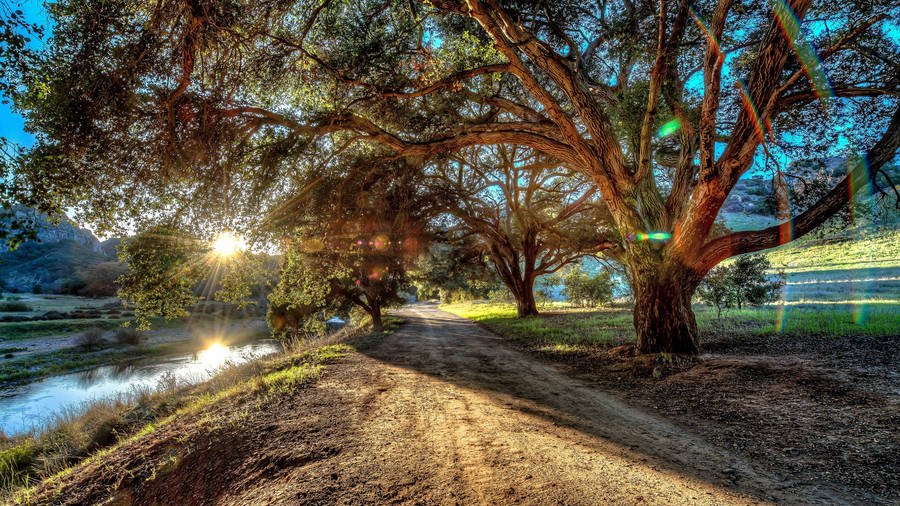
[/center]
I got one polyurethane foam spray canister with the trigger & tube to inject the material, from my local hardware store. Because cleaning the plastic injecting tube would be quite difficult when the polyurethane foam begins to be polymerized after contact with air, I cut the plastic pipe and replaced it with a straw which I threw out after each use.
[center]
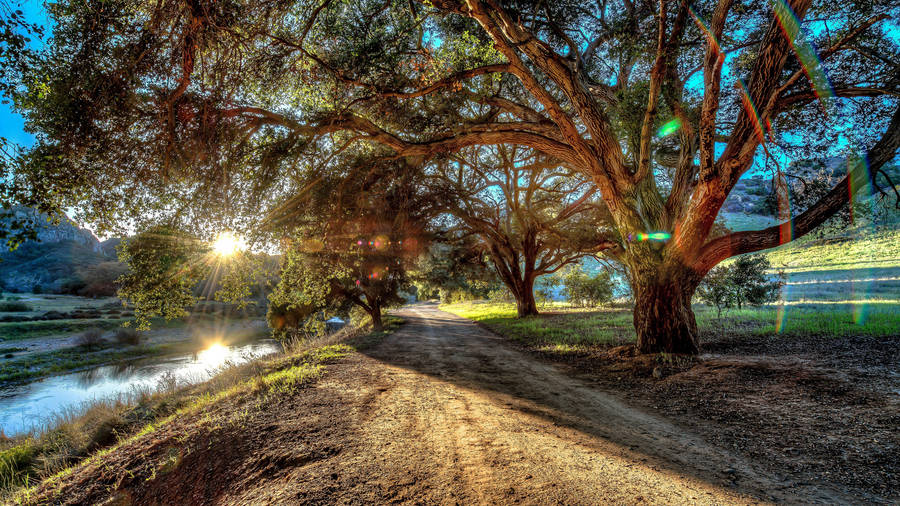
[/center]
Before channelling the polyurethane foam inside scale model, a preparation should be applied to achieve best possible results and to avoid any unpleasant surprises. I chose as the point from which will channel the polyurethane foam, the only opened hatch - the crew commander’s hatch. This is why I closed driver’s hatch, not to let polyurethane foam escape from there. Masking tape 50mm width, applied to cover the upper surface of the FDCV and protect it from possible polyurethane foam overflow.
[center]
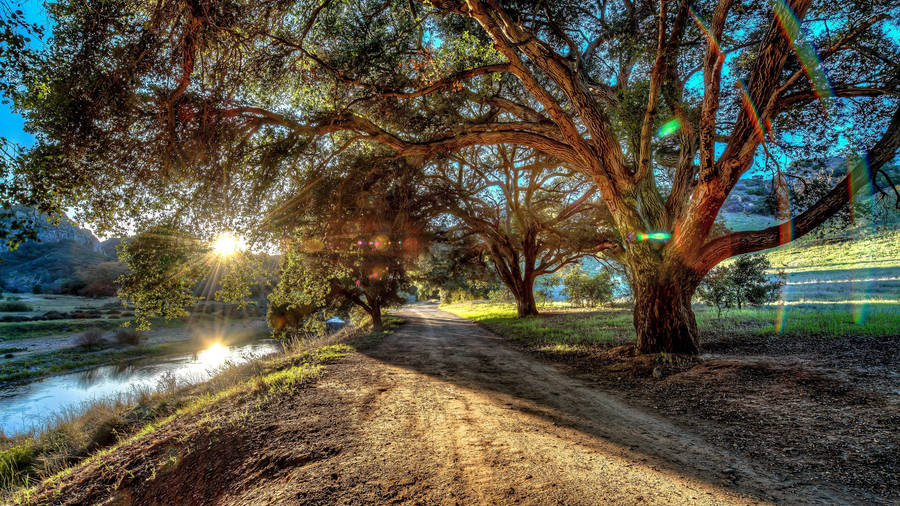
[/center]
Injecting polyurethane foam needs full attention and should not exaggerate the filling quantity because it takes time that can reach up to 2 hours from the application of the material to swell and solidify. According to the instructions on the spray canister, the best results are achieved when sprayed successive small amounts of foam and wait to swell and partially occupy all the available volume inside the model. Considering that the expanding polyurethane can multiply the original foam volume up to 4 times, it would be very appropriate to inject small quantities, allow time to swell and since we are confident that it has solidified and will not change over its volume, to continue the process with successive small amounts of foam. To conclude the process, I began to inject small amounts of polyurethane foam, first in the more distant spots, such as the front left or front right under the engine’s compartment etc. After the 2-3 small doses of injectable foam placed in appropriate locations, I wait enough time (over 6 hours) to swell smooth polyurethane and cover the internal volume without endangering the vessel to deform or break (worst scenario) from inside out, under high pressure on walls. Then, I added 1-2 more doses of polyurethane foam to the rear part, being careful to inject small amounts and let the material to expand slowly or escape if necessary, from the crew commander’s hatch.
[center]
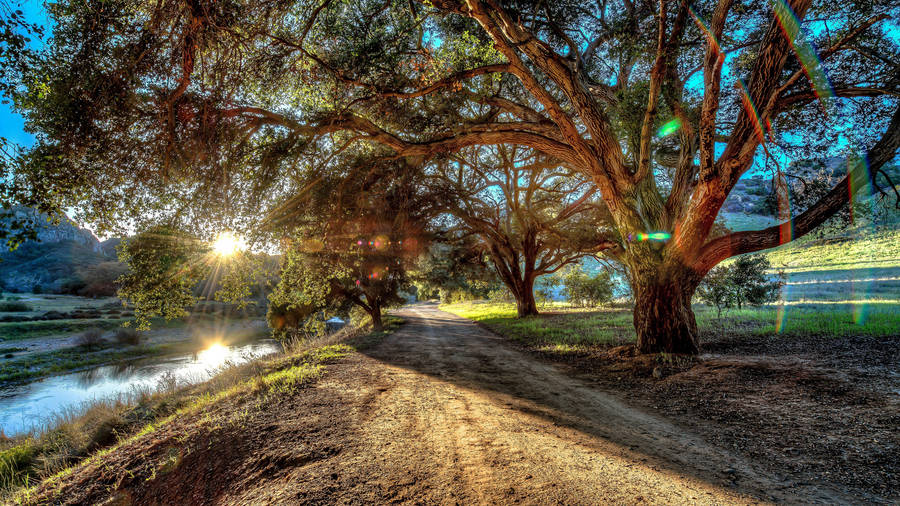
[/center]
As you can see into following picture, it seems I was lucky, because while material expanding, the polyurethane foam managed to find a way out and despite a little leaking from the driver's hatch. Although, the contact with air was quick and material became solid before escaping to the outside, covering the panel lines and kit details.
[center]
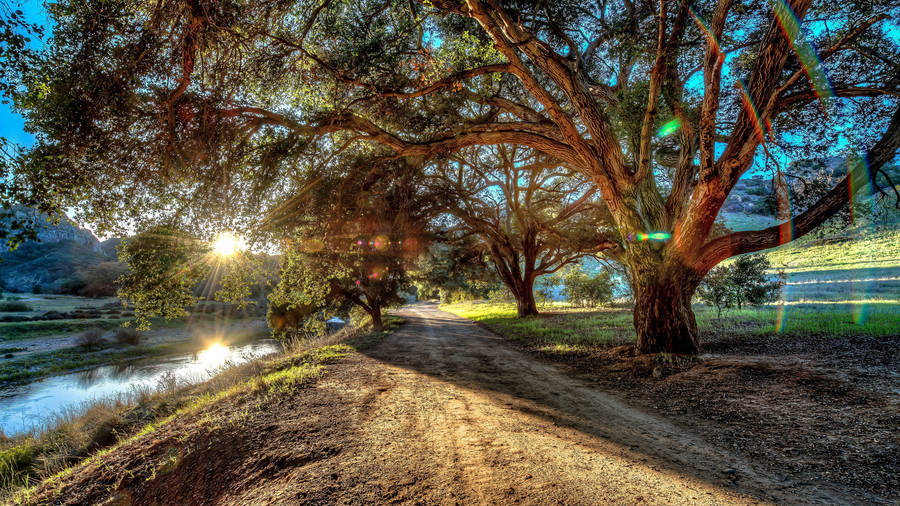
[/center]
After 3-4 small doses of polyurethane foam, with several hours stall time between injections, the material properly inflated and occupied all the available volume of the scale model’s interior. Because of wrong calculations during last injection, polyurethane foam escaped from the nearest (and only) way out - the crew commander’s hatch. Fortunately, this was the last dose and the excess was removed quickly with a spatula, while having established such a case, the protective coating of the outer surface with masking tape, proved thoughtful choice.
[center]
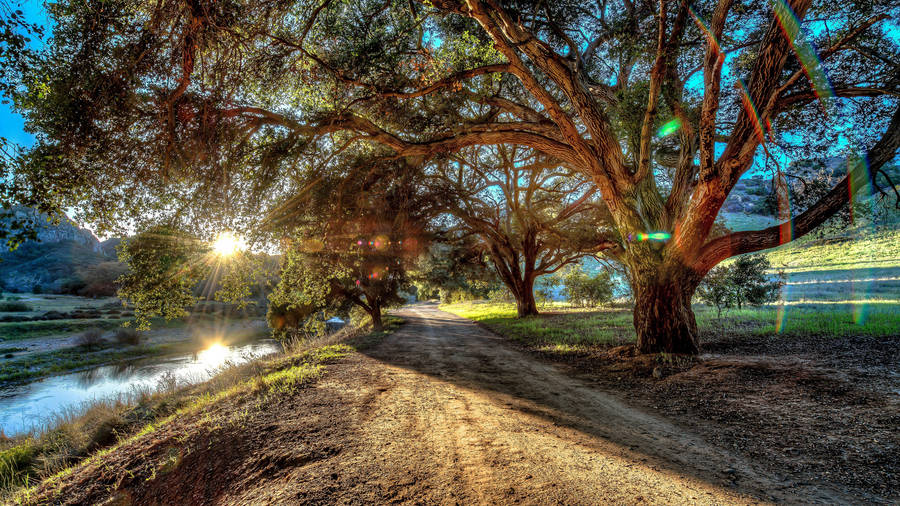
[/center]
After the last dose of polyurethane foam hardened, the excess material overflow from the driver's and crew commander’s hatches were removed carefully, using No 11 blade on modeling knife.
[center]
[/center]
With the method described in the previous paragraphs, I achieved to:
- Fill the interior of the FDCV scale model with foam that can absorb vibrations and distribute throughout the mass of polyester,
- Apply a hard duty adhesive tape across the inner surface, to hold united the shattered parts of polyester if ever broken.
The above protection measures, are not necessary (and possibly not recommended) for use on 99% of commercial kits marketed. The polyester material specificity however and the possible danger to break after few months or years, after losing its elasticity and becoming harder and inflexible (and therefore fragile), enforce these protecting measures to ensure better luck VS possible shock hits & hard vibrations during scale model transport.
Aceasta postare a fost editata de Nick_Karatzides: 02 July 2010 - 07:01 PM